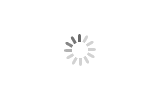
- Juncheng
- China
- 60 days to 120 days
- 50sets/month
The machine is equipped with "CP” automatic measurement system,which can perform in-process and post-process measurements.The system can be used to measure the diameter, roundness, concentricity, cylindricity and profile etc.of the workpiece.All of the measurement results can be observed in the screen and printed.
All of the measurements are performed with two measuring arms before & after the grinding. And all of the measurements can be combined with the grinding program to perform automatical operation. To avoid the false operation, all of the movements and measurements of the measuring head should be carried out automatically, not be disturbed by the operater.
All the optical scales are HEIDNAIN from Germany,and its accuracy is 1-5 um, 0.5-1 um.
Large Mill Roll CNC Grinding Machine(max dia. 3m)
HEAD STOCK
The workpiece is driven by SIEMENS motor,which performs the stepless speed regulation via SIEMENS servo speed regulation equipment SI20. It is driven by the three step V belt pulley, and the loosen & tighten of the pulley is adjusted by the eccentric sleeve and oscillating mechanism, and every step pulley is adjusted conveniently. A self-aligning driving device is mounted on the face plate to ensure rotation of workpiece stable.
TAIL STOCK
The structure of the steady is two supportpoint style. The support shoe can be adjusted manually by y a indicated scale according to the workpiece diameter. The longitudinal position of the steady can be adjusted easily. A lubricating device is mounted on the top of the support shoe to avoid high temperature while running.The left steady can be thought as U1 axis, which can make a micro adjustment for position error to make sure parallelism between centerlines of the workpiece and the workpiece machine bed( special order).
Wheel Head
The cross infeed of wheelhead consists of closed plasticcoated hydrostatic guideway, and it is driven by ball screw, which features high infeed sensitivity, good anti vibration,steady movement and nonabration of guideway.The wheel spindle adopts hydrostatic eccentric sleev and hydrodynamic bearing structure, the front and rear bearings of spindle is setted in the stressed centre of grinding wheel and the pulley respectively, and both the belt tension and grinding force of the wheel act on the center of the bearing to ensure the min.deflection, and it features high stiffness. It's suitable for rough grinding with heavy load high efficiency and fine grinding with high accuracy & high surface finish.
The grinding wheel spindle is driven by a SIEMENS motor, which performs the stepless speed regulation via SIEMENS servo speed regulation equipment SI20, and it is driven by the poly V belt.
Buildin-type wheel auto balancer is mounted inside the wheel spindle to balance the grinding wheel automatically.
Carriage
The carriage adopts V-flat plastic-coated guideway, and the difference between the center- linesof the guideway. The hydrostatic guideway oilcharmer adopts H-type special structure with the good stressed force and high stiffness. The speed of the large carriage has no effect on carriage floating with good lower speed characteristic and without creeping. The carriage guideway oil pressure adoptscapillary throttle style, and the floating amount of the carriage can be controlled via regulation of pressure.
Steady
The structure of the steady is two supportpoint style. The support shoe can be adjusted manually by a indicated scale according to the workpiece diameter. The longitudinal position of the steady can be adjusted easily.
A lubricating device is mounted on the top of the support shoe to avoid high temperature while running.
The left steady can be thought as Ul axis, which can make a micro adjustment for position error to make sure parallelism between centerlines of the workpiece and the workpiece machine bed( specialorder).
GRINDING WHEEL MACHINE BED AND WORKPIECE MACHINE BED
Workpiece and grinding wheel machine beds use vibrationisolation design for large-sized machine bed, namely workpiece and grinding wheel machine beds are seperated,which can avoid the mutual effect between the independent shaking resources of the workpiece machine body and grinding wheel machine body.
The two machine beds adopt the V and flat guideway,and the section adopts trapezidal structure, the stiffness of this structure is higher than the traditional rectangular structure.The machine bed adopts casting with low alloy, high intensity and low stress gestated cast and high hardness.
A steel elastic guard is mounted on the grinding wheel machine body to protec the guideway.
Hydraulic system
This system consists of hydraulic system for spindle and hydrau- licsystem for carriage, and Lexroth products from Germany are used for the main hydraulic pumps and vavles. The spindle hydraulic system provides the oil to grinding wheel spindle and the oil temperature control cabinet are used to control the oil temperature to be in the range of 20 ℃ ±2,which make the hydrodynamic & hydrostatic bearing be much more reliable. And carriage hydraulic system is used to control the floating amount.
MULTIFUNCTION CNC MEASUREMENT SYSTEM
The machine is equipped with "CP” automatic measurement system,which can perform in-process and post-process measurements.The system can be used to measure the diameter, roundness, concentricity, cylindricity and profile etc.of the workpiece.All of the measurement results can be observed in the screen and printed.
All of the measurements are performed with two measuring arms before & after the grinding. And all of the measurements can be combined with the grinding program to perform automatical operation. To avoid the false operation, all of the movements and measurements of the measuring head should be carried out automatically, not be disturbed by the operater.
All the optical scales are HEIDNAIN from Germany,and its accuracy is 1-5 |x m,0.5-1 |jl m.
ADVANCED SIEMENS 840DSLCNC SYSTEM
Siemens 840DSL CNC system is adopted to achieve man/machine dialogue, programming, data input, CNC measurement, compensation grinding, data processing etc.. 15,TFT CTR with fault diagnosis and printing function.The PLC (S7-300) is integrated in system to perfonn inproceww and machine logic control.
Machine adopts the Siemens S120 digitai AC servo system to drive carriage, wheelhead, middle high spindle(UI), measureing head and closed loop control can be performed in positioning control by optical scale. Position control can be easily realized by Siemens 840D system.
Windows 7 operating system is used with friendlly open Chinese interface and throughs the TFT CTR and touch soft key to realize man/machine dialogue, it is easy for operator to use. CNC long-distance diagnoses function (Using telephone modem) will achieve software update, program loading, program expanding, diagnoses etc..
Specification
Item | JK8430 | JK8450 | JK8463 | JK8480 | JK84100 | |
Machinning range . | Max grinding dia.(mm) | 300 | 500 | 630 | 800 | 1000 |
Distance between centers (m) | 2.5 | 4 | 3,4,5 | 4,5,6,8 | 4,5,6,7 | |
Max.weight of part(t) | 2 | 3 | 5 | 15 | 25/15 | |
Work speed (stepless) (r/min) | riso | rioo | rioo | V70 | T60 | |
Longitudinal moving speed of tailstock (mm/min) | manual | manual | manual | 1800 | 1800 | |
Supporting dia. of steady rest (mm) | 50~300 | 50*300 | 90~435 | 90~680 | 90~680 | |
Longitudinal moving speed of carriage (mm/min) | 0~7500 | 0~4000 | 0~2500 | 0~4000 | 0~4000 | |
Distance between two guideway centers of wheel bed (mm) | 850 | 465 | 650 | 1000 | 1200 | |
Wheel head | Max. horizontal stroke (mm) | 425 | 400 | 560 | 560 | 900/650 |
Horizontal rapid moving speed (mm/min) | 1000 | 1000 | 1000 | 1000 | 1000 | |
(mm/min) Continuous cross feed (mm/min) | 0.002~1.2 | |||||
Periodical cross feed (mm/stroke) | 0.002^0.12 | |||||
Electronic handwheel feed amouit (mm/p) | 0.001 | 0.001 | 0.001 | 0.001 | 0.001 | |
Wheel dimensions (O.DXWX 1 .D) (mm) | 750X60X305 | 750X75X305 | 750X75X305 | 750X75X305 | 900X100X305 | |
Wheel peripheral speed (m/s) | 35(45) | 35(45) | 35(45) | 35(45) | 35(45) | |
Mid convex (concave) amount (mm) | <1 | <1 | <3 | <3 | <3 | |
Measuring range (mm) | 50*300 | 50~500 | 100*630 | 100~800 | 150,000 | |
Workherd motor (KW) | 9 | 22 | 18.5 | 37 | 45 | |
Power of main motors | Wheel motor (kW) | 30 | 37 | 30(55) | 45(55) | 75 |
Wheel head cross feed motor (Nm) | 11.4 | 13 | 13 | 13 | 13 | |
Carriage longitudinal displacement motor (Nm) | 70 | 70 | 27 | 50 | 50 | |
Servo motor for grinding convex (Nm) | 5.2 | 5.2 | 6 | 6 | 6 |
Item | JK84125 | JK84160 | JK84200 | JQK84160 | JQK84315 | |
Machinning range . | Max grinding dia.(mm) | 1250 | 1600 | 2000 | 1600 | 3150 |
Distance between centers (m) | 5,6,7,8 | 6,7,8,10,12 | 8,10,11,12 | 5,6,7,8 | 4,5,6 | |
Max.weight of part(t) | 25 | 60 | 100 | 16/25 | 25 | |
Work speed (stepless) (r/min) | K60 | 「50 | V40 | K30 | V30 | |
Longitudinal moving speed of tailstock (mm/min) | 1800 | 1055 | 1310 | 1800 | 1075 | |
Supporting dia. of steady rest (mm) | 90”780 | 300~950 | 350~950 | 90~500 | 65~400 | |
Longitudinal moving speed of carriage (mm/min) | 0*4000 | 0~4000 | 0~4000 | 0~2500 | 0~2500 | |
Distance between two guideway centers of wheel bed (mm) | 1200 | 1200 | 1200 | 1000 | 1000 | |
Wheel head | Max. horizontal stroke (mm) | 900 | 950 | 950 | 650 | 650 |
Horizontal rapid moving speed (mm/min) | 1000 | 1000 | 1000 | 1000 | 1000 | |
(mm/min) Continuous cross feed (mm/min) | 0.002~1.2 | |||||
Periodical cross feed (mm/stroke) | 0.002~0.12 | |||||
Electronic handwheel feed amouit (mm/p) | 0.001 | 0.001 | 0.001 | 0.001 | 0.001 | |
Wheel dimensions (O.DXWX 1 .D) (mm) | 900X100X305 | 900X100X305 | 900X100X305 | 900X75X305 | 750X75X305 | |
Wheel peripheral speed (m/s) | 35(45) | 35(45) | 35(45) | 35 | 35 | |
Mid convex (concave) amount (mm) | <3 | <3 | <3 | <3 | <3 | |
Measuring range (mm) | 150~1250 | 300^1600 | 350~2000 | 150,600 | 35CT3150 | |
Workherd motor (KW) | 45 | 55 | 90 | 30/45 | 45 | |
Power of main motors | Wheel motor (kW) | 75 | 75 | 75 | 55 | 55 |
Wheel head cross feed motor (Nm) | 13 | 13 | 13 | 13 | 13 | |
Carriage longitudinal displacement motor (Nm) | 50 | 50 | 50 | 50 | 50 | |
Servo motor for grinding convex (Nm) | 6 | 6 | 6 | 6 | 6 |