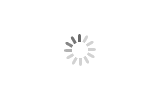
- Juncheng
- China
- 30 days to 60 days
- 50sets/month
This machine uses a diamond wheel as cutting tool, and it is mainly designed for rough, semi-fine, fine and spark-out grinding of the cylindrical surface of tungsten carbide roll and its arc-shaped slots, applied in high-speed wire production industry, with high accuracy and strong power.
Tungsten Carbide Roll Digital Display Grinding Machine
Working range:
Roll ring diameter ground: φ50~φ400mm
Max. roll ring width ground: 150mm
Working accuracy:
Outside cylindricity deviation: ≤0.005mm
Outside diameter tolerance: ±0.005mm
Roll ring root diameter tolerance: ±0.01mm
Roll slot depth tolerance: ±0.005mm
Ground surface roughness tolerance: Ra≤0.8μm
Ground surface coaxiality with regard to centering bore: ≤0.005mm
Position tolerance of center line of roll slot with regard to the end-face of roll ring: ±0.01mm
Strength of the machine:
1) The machine bed adopts integral casting structure, and is processed with aging to have good structural rigidity and accuracy retention.
2) The longitudinal and lateral movements of the machine are equipped with high-precision SPM digital display devices. The resolution of the digital display is 0.001mm. The electrical is controlled by the Siemens PLC programmable controller to realize semi-automatic circular grinding of the machine. It can also be manually operated when needed. operating.
3) The outer diameter of the diamond grinding wheel used in the machine tool is φ190 ~ φ250mm, and the maximum thickness is 65mm. The connection parameters of the main shaft extension end of the grinding wheel holder must be completely consistent with the corresponding connection parameters of the "diamond wheel dresser" to ensure that the diamond wheel after dressing can be obtained use correctly.
4) The spindle of the grinding wheel frame is supported by German FAG rolling bearings, which has the characteristics of high bearing capacity and high precision of spindle rotation. The rolling bearing lubrication system for the grinding wheel spindle is an independent, fully enclosed forced oil lubrication to ensure the service life and accuracy of the shaft system.
Optional: dynamic and static pressure bearings are used for the spindle system of the wheel carrier. The system has the characteristics of high rigidity, high precision, and strong grinding force, especially for improving the smoothness of workpiece grinding. Greatly reduce the cost of using machine tools and create more benefits.
The headstock workpiece spindle is supported by German FAG bearings, which has the characteristics of strong bearing capacity and high precision of spindle rotation.
5) The power of the motor for driving the spindle of the grinding wheel is 18.5KW, driven by the polyurethane multi-wedge belt, the speed of which is 1910r / min, the workpiece spindle is the AC variable frequency motor with gear reducer, and then driven by the three-stage reduction of the pulley and gear The work piece speed can be adjusted steplessly by AC frequency converter, and the operation is very simple.
1) The machine tool is equipped with an independent cooling system and a cooling liquid purification device, and the filtering and cooling effects are obvious.
2) The clamping of the workpiece (roller ring) uses a high-precision mandrel shaft, which makes it easy to assemble and disassemble, with high automatic centering accuracy and stable and reliable clamping.